What are the advantages of vertical machining centers and horizontal machining centers?
Vertical machining center refers to a machining center with a vertical spindle. Its structure is mostly a fixed column. The worktable is rectangular and has no indexing and rotation function. It is suitable for processing discs, sleeves and plate parts. It generally has three linear motions. Coordinate axis, and a rotary table rotating along the horizontal axis can be installed on the worktable to process spiral parts.
The vertical machining center is easy to install, easy to operate, easy to observe the processing conditions, easy to debug the program, and widely used. However, due to the limitation of the height of the column and the tool changer, parts that are too high cannot be machined. When machining the cavity or the concave profile, the chips are not easy to discharge. In severe cases, the tool will be damaged and the machined surface will be damaged, which will affect the smooth processing. .
Horizontal machining center refers to a machining center with a horizontal spindle. It usually has an automatic indexing rotary table. It generally has 3 to 5 motion coordinates. The common one is three linear motion coordinates plus one rotary motion coordinate. After the card is installed once, the processing of the remaining four surfaces except the mounting surface and the top surface is completed. It is most suitable for adding box parts. Compared with the vertical machining center, the horizontal machining center is easy to remove chips during machining, which is beneficial to the machining, but the structure is complicated. The price is higher.
Simply put, the lubrication system of the vertical machining center is to mix the separately supplied lubricating oil and compressed air to form a turbulent air-gas mixed flow and then supply it to the main shaft part of the machining center or other lubrication parts.
Features of vertical machining center:
1. Environmental protection and no pollution. Because there will be no oil and mist sprayed out, the surrounding environment is not polluted.
2. Accurate oil supply. The oil can be delivered to the lubrication points such as the spindle and screw according to different needs by adding a regulating valve;
3. There is no problem of difficulty in atomization of high-viscosity lubricating oil; suitable for any oil;
4, automatic detection and monitoring. It can detect whether the lubricating oil is normal. If the lubrication is poor, it can alarm and stop to avoid abnormal operation of the equipment.
5. It is especially suitable for the rolling bearing of the main shaft. It has a certain air cooling effect, which can reduce the operating temperature of the bearing, thereby extending the service life of the main shaft;
6. Low fuel consumption and cost saving.
The similarities and differences between oil-air lubrication and oil mist lubrication:
The same point: all are powered by compressed air.
Different points: Oil-air lubrication does not smash oil into broken mist, but uses compressed air flow to transport small oil droplets along the pipeline to the lubrication point.
Oil-air lubrication has many advantages compared with other lubrication. The oil and gas lubrication system of the machining center mainly consists of pneumatic pumps, air source processing components, control parts, spiral pipes and other accessories. Unlike oil mist lubrication, oil-air lubrication uses a wide range of oil viscosity.
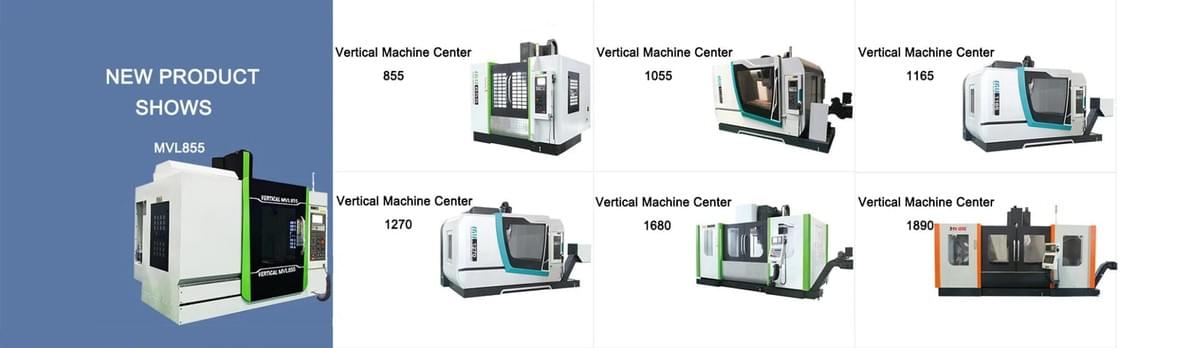